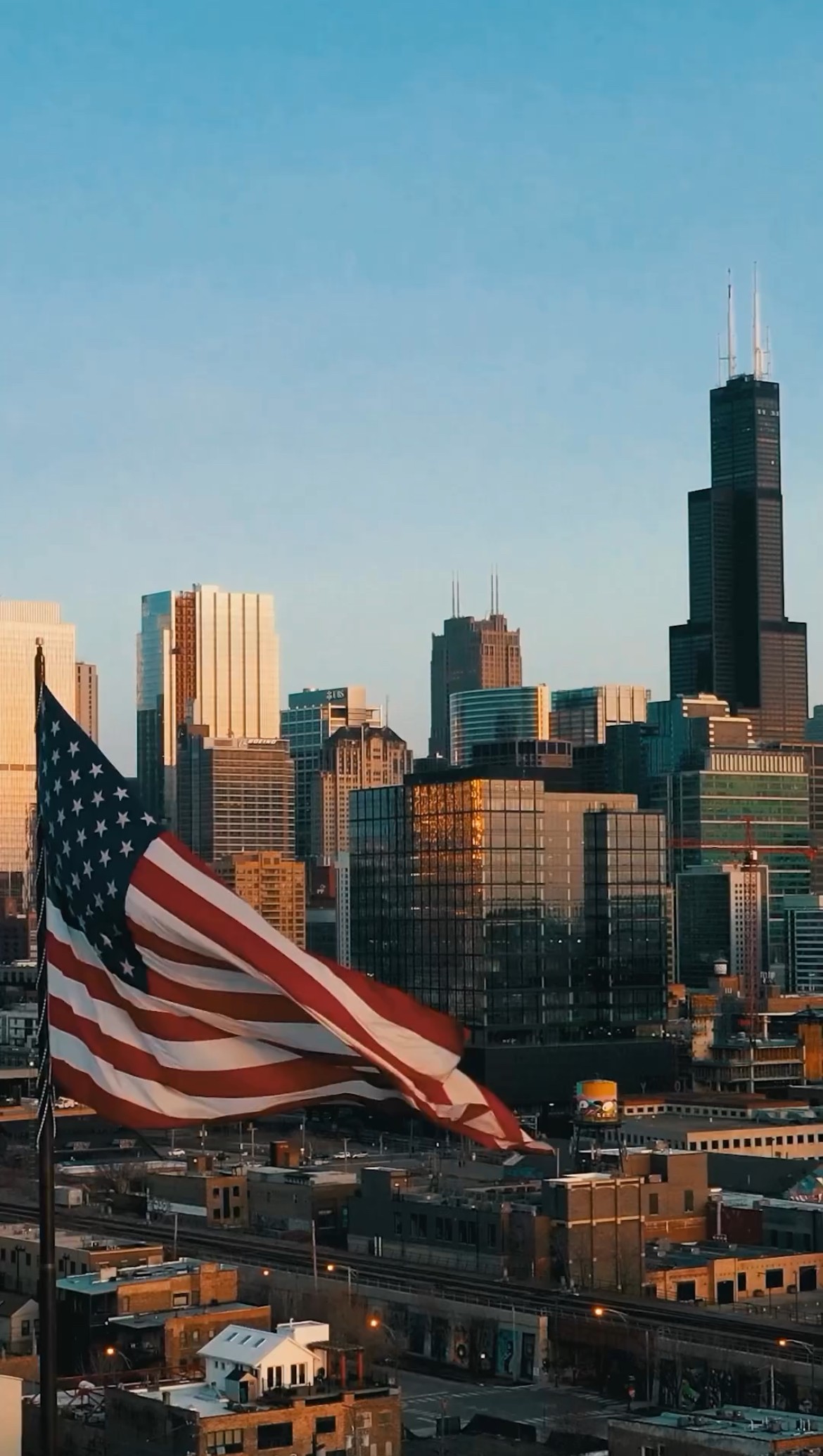
ADDITIVE MANUFACTURING
Revolutionizing the Defense Industry
Read more
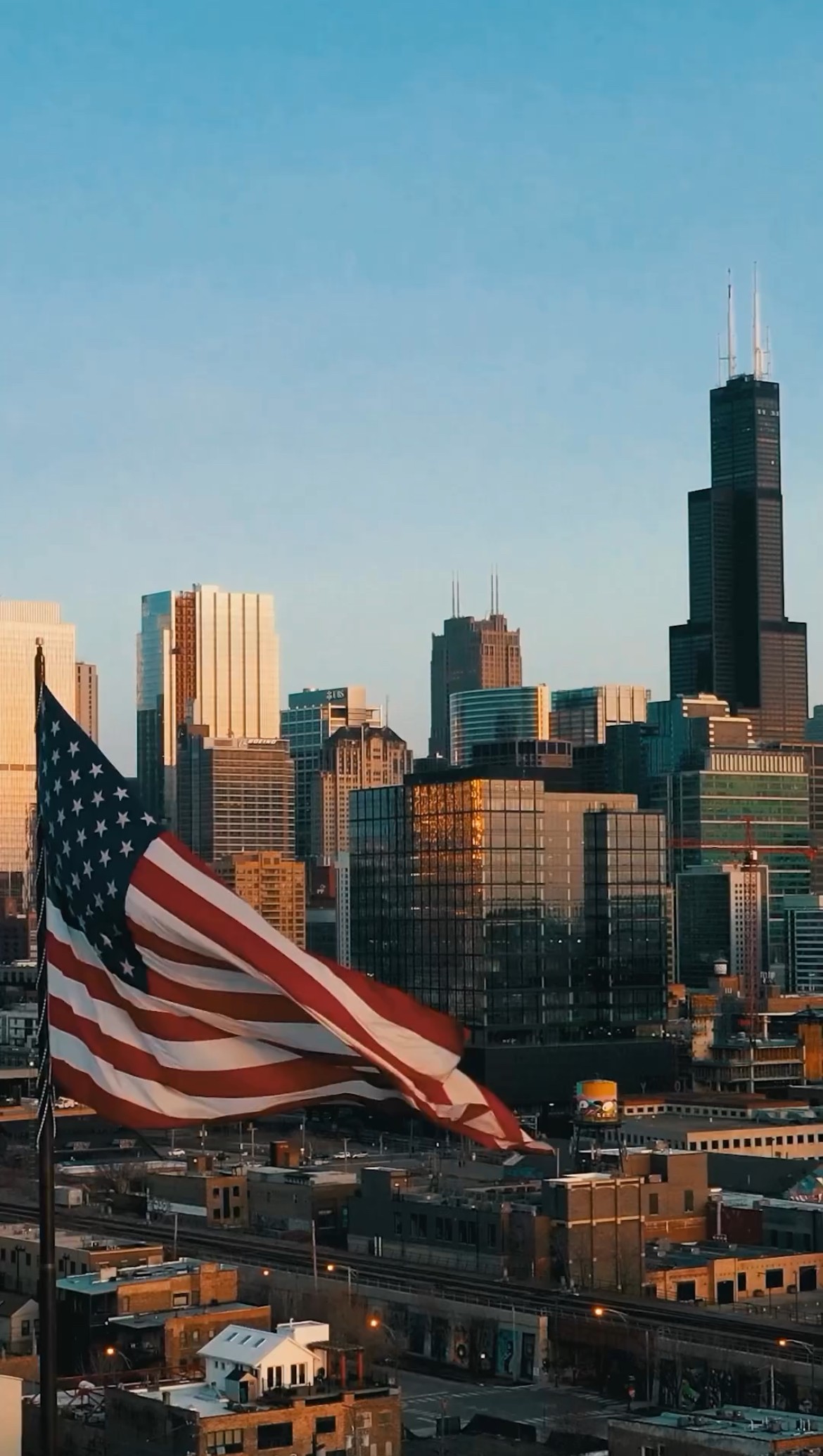
ADDITIVE MANUFACTURING
Revolutionizing the Defense Industry
Read more
How Additive Manufacturing is Revolutionizing the Defense Industry
Defense
|
2024
Additive manufacturing (AM), or 3D printing, is reshaping the defense industry. The technology's ability to produce highly complex, lightweight, and durable parts quickly is driving innovation across industries, from automotive to aerospace.
This shift is particularly crucial as the defense sector grapples with the challenges of global supply chain disruptions and seeks to enhance national security capabilities.
Additive Manufacturing's Disruptive Capabilities
Customization and Rapid Prototyping
AM allows for customized parts without the need for expensive tooling or dyes, making it ideal for rapid iteration and testing of new weapons systems. This allows defense manufacturers to significantly reduce development cycles and time-to-market.
Sig Sauer, a leading Department of Defense supplier, has embraced AM during the development of its pistols, rifles, and silencers. AM enables silencers to be printed in one piece, using advanced materials to reduce weight and improve sound suppression.
Enabling Rapid, On-Site Repairs
With 3D printers, defense contractors can produce parts closer to the point of need—whether in a remote base or in the field. This is invaluable for reducing downtime and improving operational readiness.
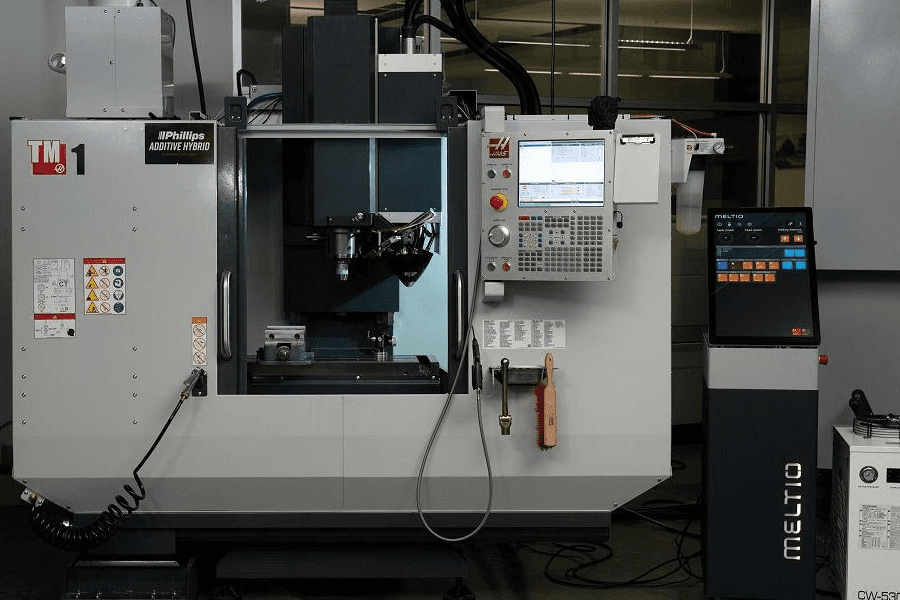
The U.S. Navy uses AM on its USS Bataan to produce ship parts like water filters at sea, cutting costs by up to 98% and reducing wait times for supplies. On-site production shortens lead times, addresses obsolescence, and boosts operational self-sufficiency.
Reducing Supply Chain Vulnerabilities
AM allows for the localized production of parts, reducing reliance on global supply chains and mitigating risks from geopolitical or pandemic-related disruptions.
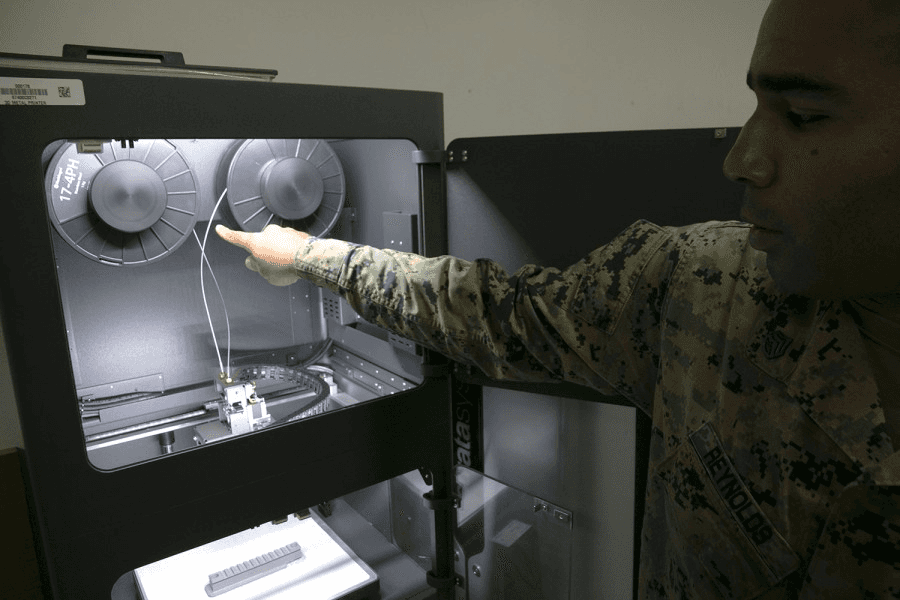
The U.S. Army has deployed Markforged composite printers at base locations to manufacture vehicle parts, tools, and personal protective equipment (PPE), ensuring a steady supply of critical components without relying on foreign suppliers.
Addressing Design Vulnerabilities
AM allows for the production of parts with fewer physical weaknesses than those made through traditional methods, especially in complex systems like combat vehicles.
The U.S. Army's Jointless Hull Project uses AM to print seamless, single-piece combat vehicle hulls. This eliminates weak points like welded joints, improving the vehicle’s resistance to roadside bombs and underbody blasts.
Advanced Materials
AM enables the use of high-performance materials like titanium and carbon-fiber-reinforced polymers. This allows for the creation of complex, lightweight, and highly durable products that traditional methods could not achieve.
The Army Research Laboratory is experimenting with lightweight metals to improve vehicle components, while also reducing the burden on soldiers who carry up to 140 pounds of gear in the field.
Real-World Impact: Military AM Projects
Construction-Scale Printing
The Army Corps of Engineers has been working since 2015 to develop technology that can print large-scale structures like buildings and bridges. The Additive Construction Program has successfully produced multiple 3D-printed buildings and structures, reducing labor costs and construction times while improving structural integrity.
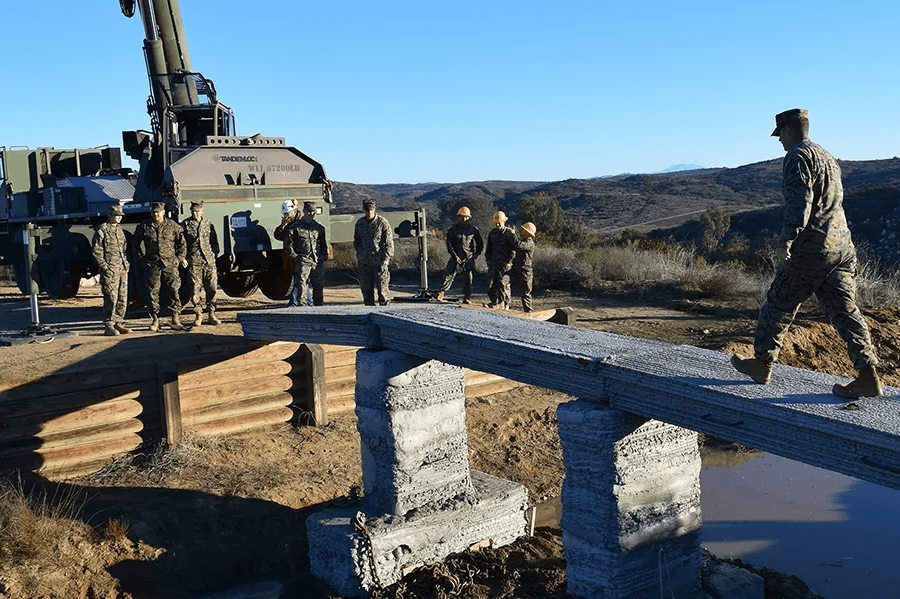
Field-Ready Printing
Military forces are also exploring the use of rugged 3D printers that can operate in remote or hostile environments. These machines could enable soldiers to print replacement parts or equipment on the battlefield, using materials like recycled plastics found on site.
AM Forward Initiative
To accelerate domestic AM adoption, the U.S. government launched the AM Forward initiative in partnership with industry giants like GE Aviation and Lockheed Martin.
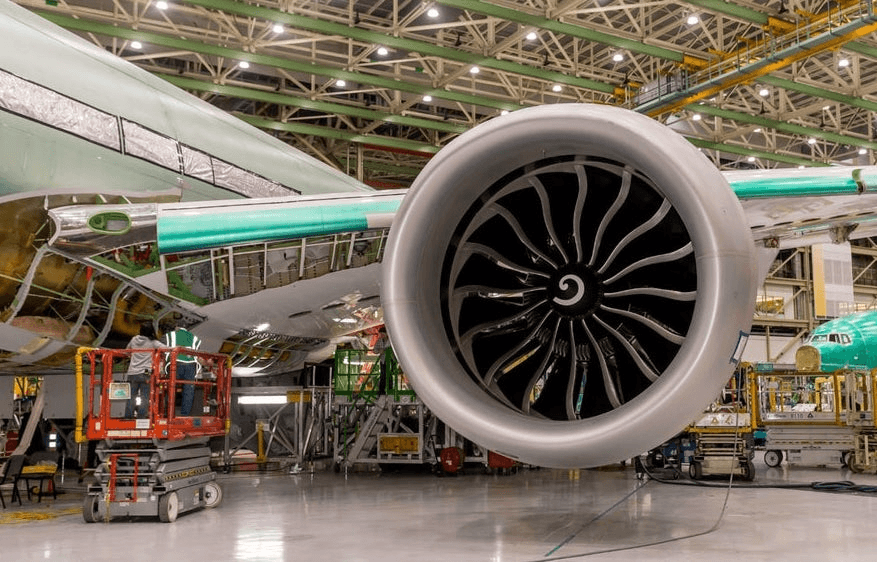
This program helps small- and medium-sized manufacturers adopt AM technologies through investment and training, boosting domestic production and reduce reliance on foreign supply chains.
Challenges of Adopting AM
Despite its clear advantages, several challenges hinder the widespread adoption of AM in these industries:
High Upfront Costs: While large defense contractors have embraced AM, smaller companies face financial hurdles in adopting the technology due to its significant initial investment.
Lack of Industry Standards: The defense industry lacks consistent standards for AM processes and materials, which hampers broader adoption. AM Forward is working to create new standards that ensure reliability and quality.
Material Limitations: While AM allows for the use of advanced materials, printing high-performance metals and composites consistently remains a technical challenge.
Skilled Labor Shortage: The specialized knowledge required to operate 3D printers and optimize designs for AM is in short supply. Industry efforts are underway to bridge this skills gap through training and certification programs.
Additive manufacturing is reshaping the defense industry by enabling rapid prototyping, localized production, and enhanced design capabilities. While challenges remain, the potential for AM to revolutionize defense logistics, improve equipment durability, and boost operational flexibility is clear.
About White Collar Combat
White Collar Combat provides finance and strategy consulting for the firearms, defense, technology, and manufacturing sectors.
We help companies assess the financial impact of adopting additive manufacturing, optimize capital allocation, and develop strategies that drive cost efficiency and long-term profitability.
Contact us today to ensure your business is financially positioned to leverage additive manufacturing technologies and stay competitive in an evolving defense landscape.
Additive manufacturing (AM), or 3D printing, is reshaping the defense industry. The technology's ability to produce highly complex, lightweight, and durable parts quickly is driving innovation across industries, from automotive to aerospace.
This shift is particularly crucial as the defense sector grapples with the challenges of global supply chain disruptions and seeks to enhance national security capabilities.
Additive Manufacturing's Disruptive Capabilities
Customization and Rapid Prototyping
AM allows for customized parts without the need for expensive tooling or dyes, making it ideal for rapid iteration and testing of new weapons systems. This allows defense manufacturers to significantly reduce development cycles and time-to-market.
Sig Sauer, a leading Department of Defense supplier, has embraced AM during the development of its pistols, rifles, and silencers. AM enables silencers to be printed in one piece, using advanced materials to reduce weight and improve sound suppression.
Enabling Rapid, On-Site Repairs
With 3D printers, defense contractors can produce parts closer to the point of need—whether in a remote base or in the field. This is invaluable for reducing downtime and improving operational readiness.
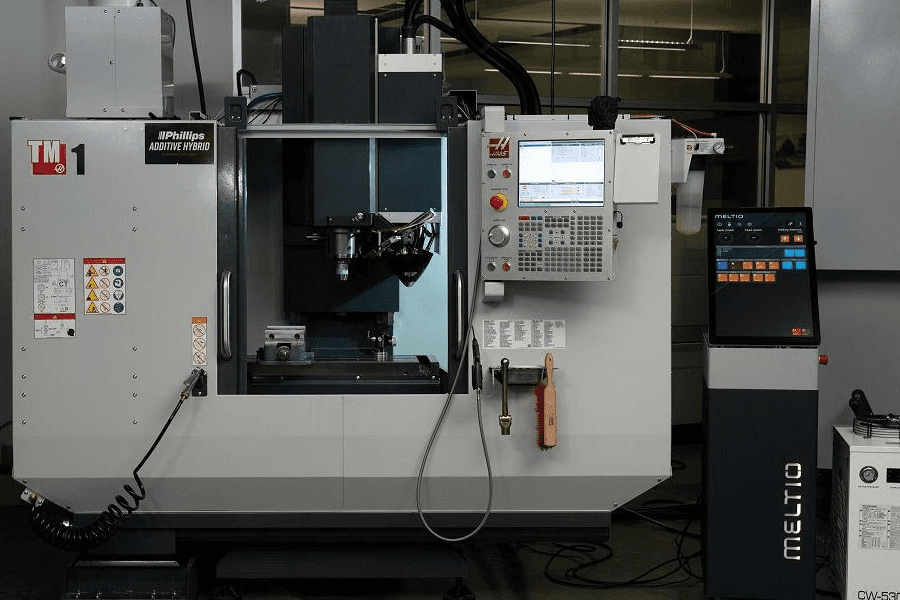
The U.S. Navy uses AM on its USS Bataan to produce ship parts like water filters at sea, cutting costs by up to 98% and reducing wait times for supplies. On-site production shortens lead times, addresses obsolescence, and boosts operational self-sufficiency.
Reducing Supply Chain Vulnerabilities
AM allows for the localized production of parts, reducing reliance on global supply chains and mitigating risks from geopolitical or pandemic-related disruptions.
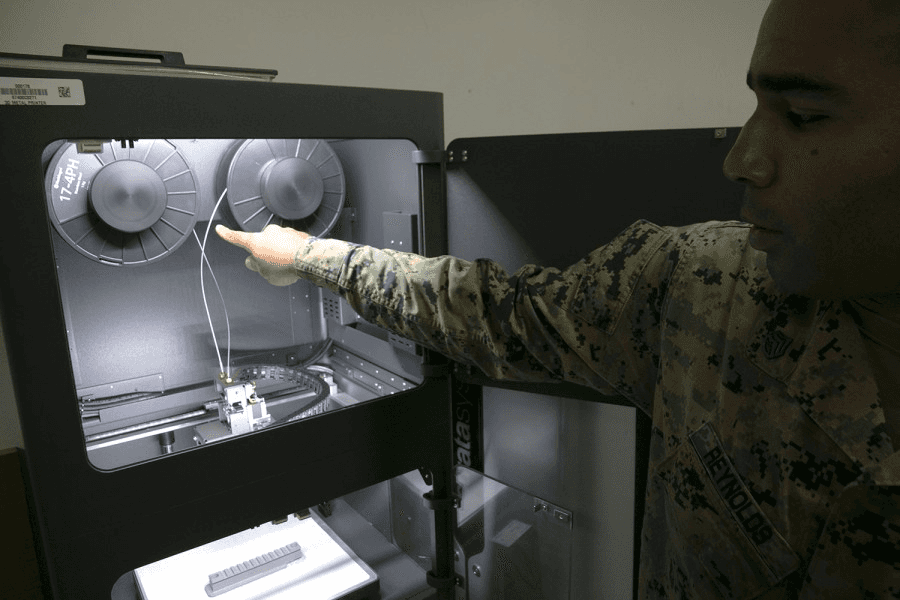
The U.S. Army has deployed Markforged composite printers at base locations to manufacture vehicle parts, tools, and personal protective equipment (PPE), ensuring a steady supply of critical components without relying on foreign suppliers.
Addressing Design Vulnerabilities
AM allows for the production of parts with fewer physical weaknesses than those made through traditional methods, especially in complex systems like combat vehicles.
The U.S. Army's Jointless Hull Project uses AM to print seamless, single-piece combat vehicle hulls. This eliminates weak points like welded joints, improving the vehicle’s resistance to roadside bombs and underbody blasts.
Advanced Materials
AM enables the use of high-performance materials like titanium and carbon-fiber-reinforced polymers. This allows for the creation of complex, lightweight, and highly durable products that traditional methods could not achieve.
The Army Research Laboratory is experimenting with lightweight metals to improve vehicle components, while also reducing the burden on soldiers who carry up to 140 pounds of gear in the field.
Real-World Impact: Military AM Projects
Construction-Scale Printing
The Army Corps of Engineers has been working since 2015 to develop technology that can print large-scale structures like buildings and bridges. The Additive Construction Program has successfully produced multiple 3D-printed buildings and structures, reducing labor costs and construction times while improving structural integrity.
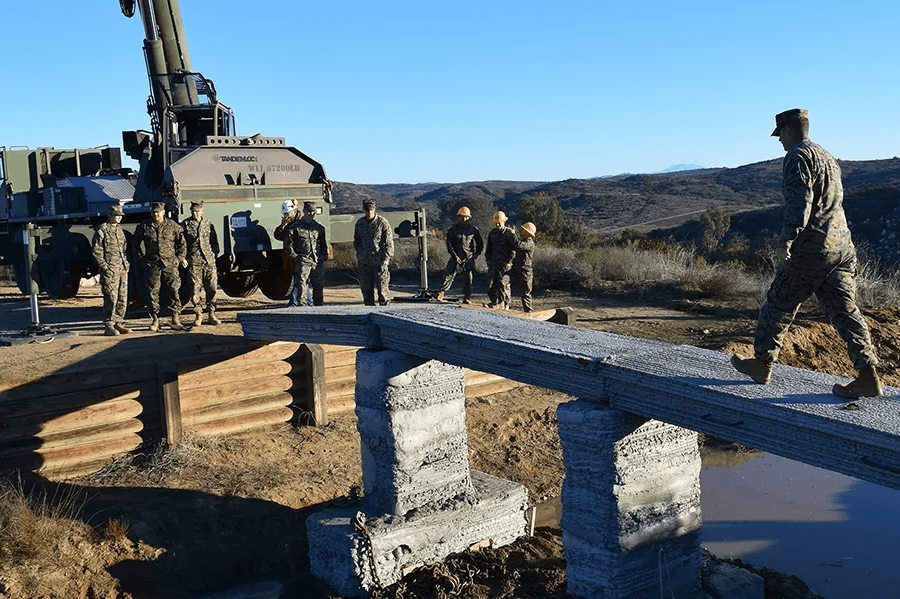
Field-Ready Printing
Military forces are also exploring the use of rugged 3D printers that can operate in remote or hostile environments. These machines could enable soldiers to print replacement parts or equipment on the battlefield, using materials like recycled plastics found on site.
AM Forward Initiative
To accelerate domestic AM adoption, the U.S. government launched the AM Forward initiative in partnership with industry giants like GE Aviation and Lockheed Martin.
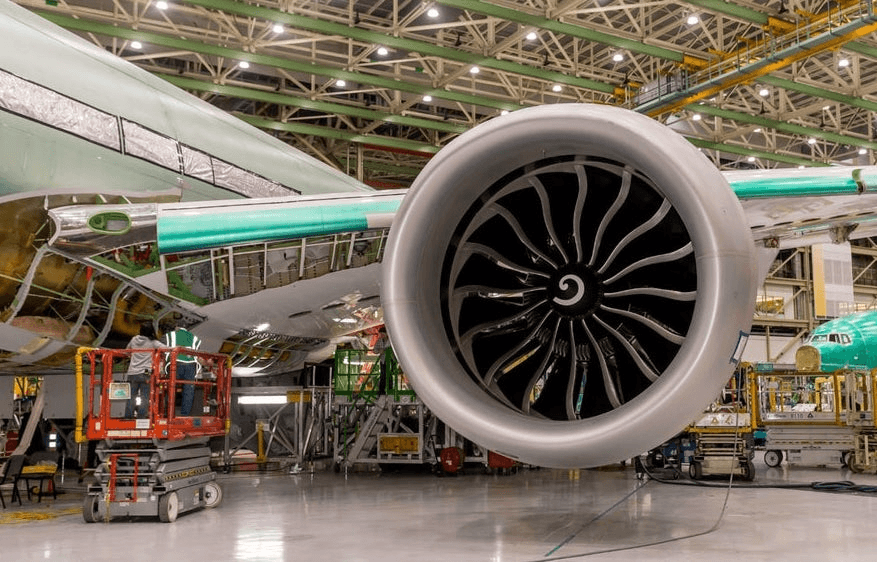
This program helps small- and medium-sized manufacturers adopt AM technologies through investment and training, boosting domestic production and reduce reliance on foreign supply chains.
Challenges of Adopting AM
Despite its clear advantages, several challenges hinder the widespread adoption of AM in these industries:
High Upfront Costs: While large defense contractors have embraced AM, smaller companies face financial hurdles in adopting the technology due to its significant initial investment.
Lack of Industry Standards: The defense industry lacks consistent standards for AM processes and materials, which hampers broader adoption. AM Forward is working to create new standards that ensure reliability and quality.
Material Limitations: While AM allows for the use of advanced materials, printing high-performance metals and composites consistently remains a technical challenge.
Skilled Labor Shortage: The specialized knowledge required to operate 3D printers and optimize designs for AM is in short supply. Industry efforts are underway to bridge this skills gap through training and certification programs.
Additive manufacturing is reshaping the defense industry by enabling rapid prototyping, localized production, and enhanced design capabilities. While challenges remain, the potential for AM to revolutionize defense logistics, improve equipment durability, and boost operational flexibility is clear.
About White Collar Combat
White Collar Combat provides finance and strategy consulting for the firearms, defense, technology, and manufacturing sectors.
We help companies assess the financial impact of adopting additive manufacturing, optimize capital allocation, and develop strategies that drive cost efficiency and long-term profitability.
Contact us today to ensure your business is financially positioned to leverage additive manufacturing technologies and stay competitive in an evolving defense landscape.
Additive manufacturing (AM), or 3D printing, is reshaping the defense industry. The technology's ability to produce highly complex, lightweight, and durable parts quickly is driving innovation across industries, from automotive to aerospace.
This shift is particularly crucial as the defense sector grapples with the challenges of global supply chain disruptions and seeks to enhance national security capabilities.
Additive Manufacturing's Disruptive Capabilities
Customization and Rapid Prototyping
AM allows for customized parts without the need for expensive tooling or dyes, making it ideal for rapid iteration and testing of new weapons systems. This allows defense manufacturers to significantly reduce development cycles and time-to-market.
Sig Sauer, a leading Department of Defense supplier, has embraced AM during the development of its pistols, rifles, and silencers. AM enables silencers to be printed in one piece, using advanced materials to reduce weight and improve sound suppression.
Enabling Rapid, On-Site Repairs
With 3D printers, defense contractors can produce parts closer to the point of need—whether in a remote base or in the field. This is invaluable for reducing downtime and improving operational readiness.
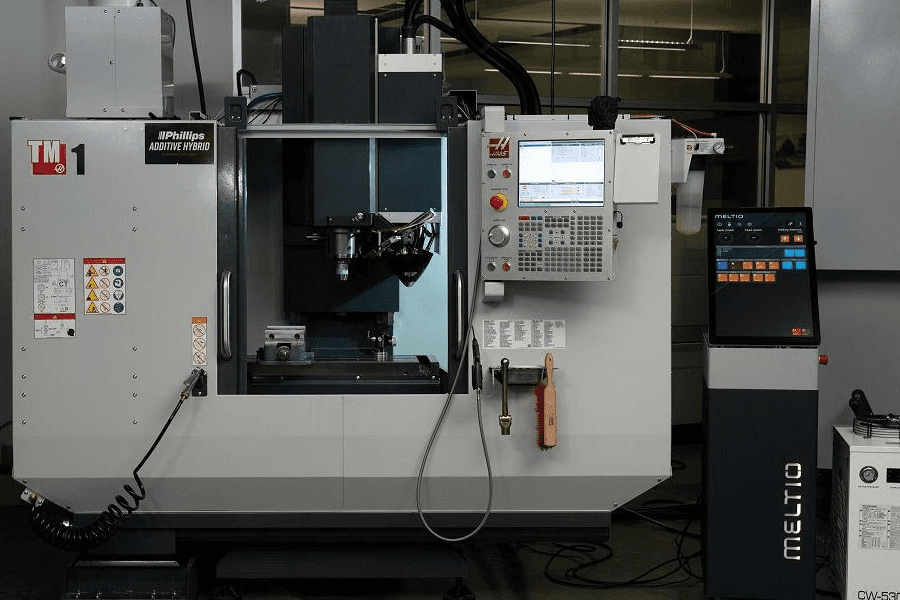
The U.S. Navy uses AM on its USS Bataan to produce ship parts like water filters at sea, cutting costs by up to 98% and reducing wait times for supplies. On-site production shortens lead times, addresses obsolescence, and boosts operational self-sufficiency.
Reducing Supply Chain Vulnerabilities
AM allows for the localized production of parts, reducing reliance on global supply chains and mitigating risks from geopolitical or pandemic-related disruptions.
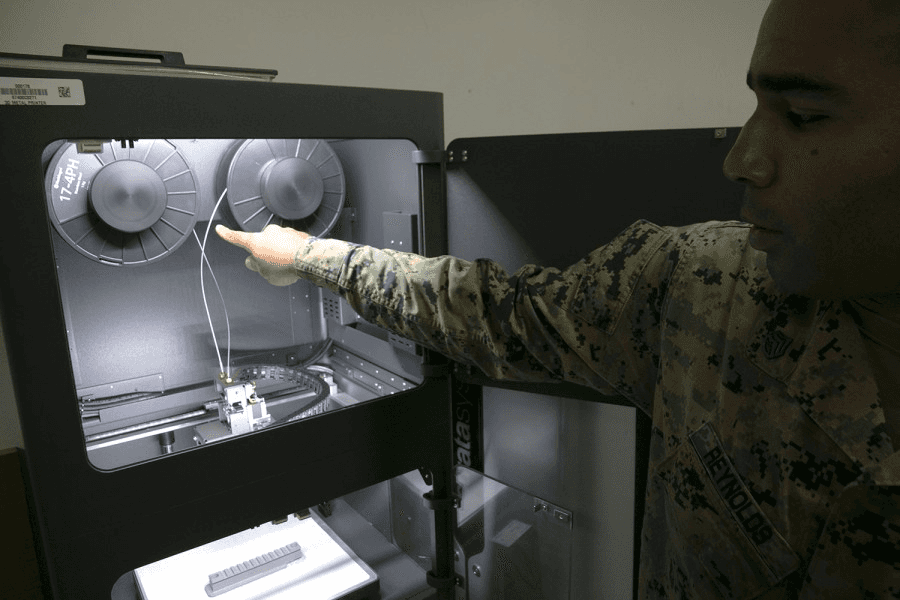
The U.S. Army has deployed Markforged composite printers at base locations to manufacture vehicle parts, tools, and personal protective equipment (PPE), ensuring a steady supply of critical components without relying on foreign suppliers.
Addressing Design Vulnerabilities
AM allows for the production of parts with fewer physical weaknesses than those made through traditional methods, especially in complex systems like combat vehicles.
The U.S. Army's Jointless Hull Project uses AM to print seamless, single-piece combat vehicle hulls. This eliminates weak points like welded joints, improving the vehicle’s resistance to roadside bombs and underbody blasts.
Advanced Materials
AM enables the use of high-performance materials like titanium and carbon-fiber-reinforced polymers. This allows for the creation of complex, lightweight, and highly durable products that traditional methods could not achieve.
The Army Research Laboratory is experimenting with lightweight metals to improve vehicle components, while also reducing the burden on soldiers who carry up to 140 pounds of gear in the field.
Real-World Impact: Military AM Projects
Construction-Scale Printing
The Army Corps of Engineers has been working since 2015 to develop technology that can print large-scale structures like buildings and bridges. The Additive Construction Program has successfully produced multiple 3D-printed buildings and structures, reducing labor costs and construction times while improving structural integrity.
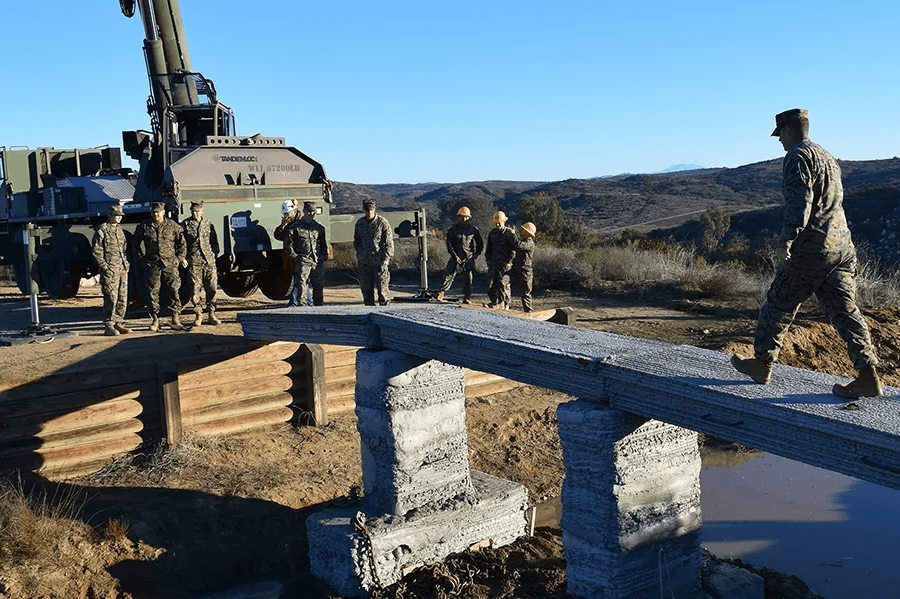
Field-Ready Printing
Military forces are also exploring the use of rugged 3D printers that can operate in remote or hostile environments. These machines could enable soldiers to print replacement parts or equipment on the battlefield, using materials like recycled plastics found on site.
AM Forward Initiative
To accelerate domestic AM adoption, the U.S. government launched the AM Forward initiative in partnership with industry giants like GE Aviation and Lockheed Martin.
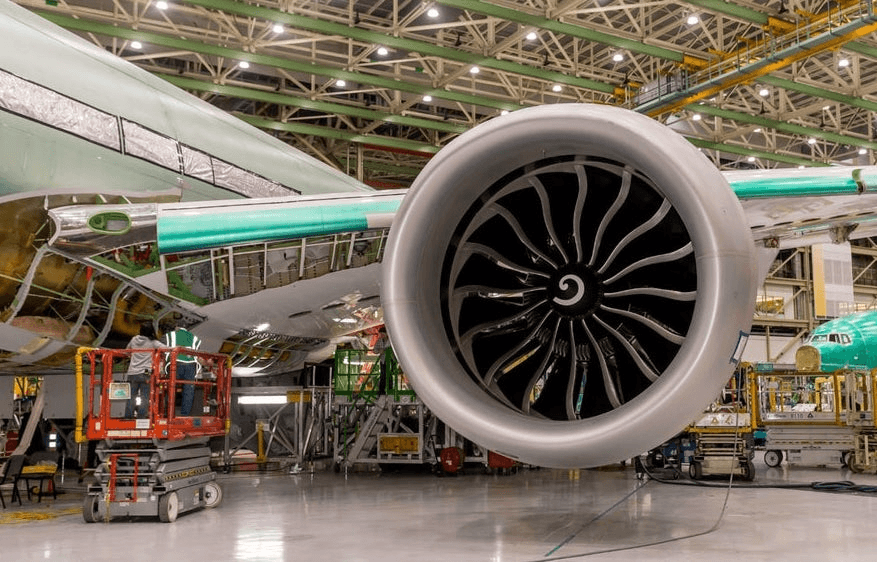
This program helps small- and medium-sized manufacturers adopt AM technologies through investment and training, boosting domestic production and reduce reliance on foreign supply chains.
Challenges of Adopting AM
Despite its clear advantages, several challenges hinder the widespread adoption of AM in these industries:
High Upfront Costs: While large defense contractors have embraced AM, smaller companies face financial hurdles in adopting the technology due to its significant initial investment.
Lack of Industry Standards: The defense industry lacks consistent standards for AM processes and materials, which hampers broader adoption. AM Forward is working to create new standards that ensure reliability and quality.
Material Limitations: While AM allows for the use of advanced materials, printing high-performance metals and composites consistently remains a technical challenge.
Skilled Labor Shortage: The specialized knowledge required to operate 3D printers and optimize designs for AM is in short supply. Industry efforts are underway to bridge this skills gap through training and certification programs.
Additive manufacturing is reshaping the defense industry by enabling rapid prototyping, localized production, and enhanced design capabilities. While challenges remain, the potential for AM to revolutionize defense logistics, improve equipment durability, and boost operational flexibility is clear.
About White Collar Combat
White Collar Combat provides finance and strategy consulting for the firearms, defense, technology, and manufacturing sectors.
We help companies assess the financial impact of adopting additive manufacturing, optimize capital allocation, and develop strategies that drive cost efficiency and long-term profitability.
Contact us today to ensure your business is financially positioned to leverage additive manufacturing technologies and stay competitive in an evolving defense landscape.
Contact
© White Collar Combat 2024
Contact
© White Collar Combat 2024
Contact
© White Collar Combat 2024